This is the third article in a series of articles outlining the must-know factors when dimensioning a variable frequency drive for a drive system. This article explains how to read a motor nameplate and why knowing how to read a motor nameplate is crucial for avoiding motor failure in a drive system. Read our other articles in this series on dimensioning for different load characteristics and power supply.
Before choosing a variable frequency drive (VFD), you need to choose an appropriate 3-phase motor. The motor must be of the correct voltage and frequency – the usual way to determine this is by using the motor manufacturer’s own technical data, much of which will be stated on the motor nameplate.
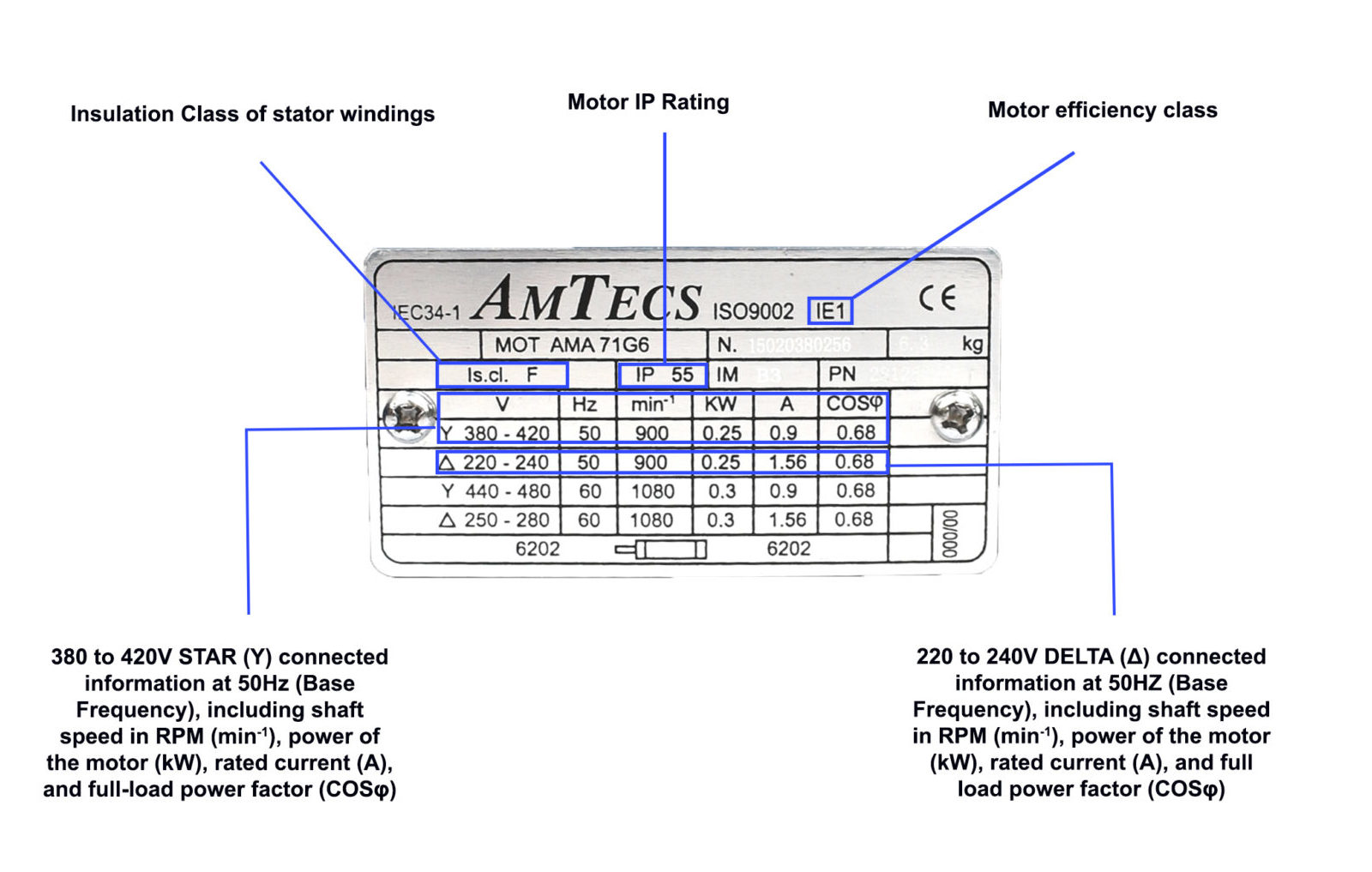
Figure 1: A motor nameplate example
The manufacturer’s data and the motor nameplate normally displays the following information:
- Voltage, phase number and frequency
- Power and current rating
- Power Factor and Insulation Class
- IP rating
Motor types
There are two popular general purpose AC motor types:
- the synchronous motor-based on a permanent magnet rotor design; and,
- the asynchronous or induction motor.
The asynchronous or induction motor still remains the most widely used of the two – across a wide variety of applications.
Motor configurations
Inside the motor connection box of a standard dual-voltage induction motor there will normally be six studs visible to which each end of the three stator windings are connected. For VFD or DOL operation. These studs must be connected together in either one of two possible configurations known as STAR (YY) or DELTA (Δ), see below:
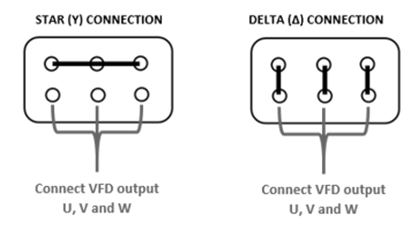
Always read and understand the motor rating plate before connecting to a VFD. Make sure the motor is configured correctly before applying power.
It is important to connect the motor as instructed on the rating plate and according to the supply voltage (VFD rated output voltage). Failure to do so can cause motor stator winding failure and/or cause the VFD to trip or fail. The motor may also be unable to deliver rated torque and speed or operate at excessive current.
Selecting a motor: key considerations
Torque & thermal overloading
Motors must be able to supply sufficient shaft torque for the required application. This applies across the desired speed range and allows for any expected overloads – without exceeding its thermal capabilities. A margin of around 30% for the motor’s maximum torque is typical in the dimensioning phase.
Low-speed operation
Using a variable frequency drive brings the possibility of low-speed, high-load operation. If, for example, a heavy-duty load needs to be driven at a low speed, while operating at a high load current, this needs to be taken into account.
In this scenario, the cooling fan attached to the non-drive end of the shaft may not keep the stator windings within designed temperature limits. To avoid over heating the motor stator windings a separately excited, forced air cooling fan should be mounted onto the none drive end of the motor.
If the load is very heavy or prone to step changes, you may also need an appropriate rotary encoder fitted to the motor shaft. This will enable the VFD to accurately control the motor speed from zero to maximum required under rapidly fluctuation load conditions.
Stator windings: a common cause of failure
When a VFD is installed, excessive overheating of the stator windings is one of the most common causes of motor failure. To supplement forced cooling, Class F insulation (as a minimum) should be specified when ordering the motor.
Efficiency – Eco-design Regulation 2019/1781
Regulations introduced in 2016 by the European Union also specify a minimum allowed motor efficiency, under the Ecodesign Regulation (Directive 2019/1781). This comes into effect on 1st July 2021, which means all new designs must comply with the regulation from then on.
The regulation covers all 2, 4, 6 and 8 pole induction motors between 0.75kW to 1,000kW. One of the most notable changes is that a low-efficiency motor can no longer be driven from a VFD – which makes choosing the right motor all the more important.
Key takeaways
- Understanding the motor specifications are essential for ensuring against motor failure in a drive system
- Five of the highest priorities you need to consider while selecting an appropriate motor:
- Voltage, phase number, frequency and power rating
- Shaft torque across the required speed range
- Thermal overloadability
- Will the motor be operated at low speed?
- Minimum motor efficiency – Ecodesign Regulation (2019/1781)
Dimensioning a drive system? Dalroad is here to help.
Dalroad supports end users and electrical contractors in a wide variety of industries to dimension their drive systems and choose the best variable frequency drive for their project. Whether you are working on a fan or pump, or a heavy-duty application, we’re able to offer our customers best-in-class support from dimensioning to installation.
Get in touch with an inverter drives expert at Dalroad today for no-obligation advice and product recommendations.