Contactors
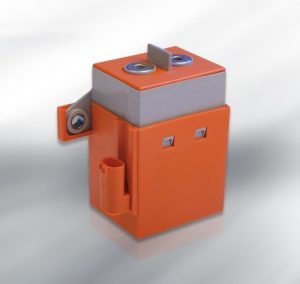
Contactors are multi-functional components, built to fulfil the requirements of various systems. A main contactor, for example, is used to connect and disconnect the traction battery from the electric drivetrain. A key function of contactors is that they make the motor drive electronics as safe as possible, during regular use and in a crash situation.
Functional contactors are of particular importance in very high voltage machines, where a potentially damaging, extremely high current short circuit might occur, resulting in fire.
In a high voltage machine, a contactor will have to handle dangerous voltages, reliably. One such component that is up to the task, is the TE EVC 250-800 Contactor, which is designed with a rated load voltage of 800V. The high voltage contactor is designed to be used in a full range of electric vehicles: including hybrid, full-electric and fuel cell vehicles.
The part has a voltage rating of up to 800VDC, and a continuous current of 250A, it also has a safe short circuit carry capability of 6k and is designed to comply with demanding switching requirements in hybrid and electric vehicles.
Unlike traditional contactors, TE’s range work without a gas-filling. A disadvantage of gas-fillings is that they bear the risk of rupture when strong arching generates excess gas pressure inside the contact chamber.
While gas-free, the contactor is still protected against pollution, it allows for gas exchange and an equalization of inside and outside pressure. This practically eliminates the risk of rupture in the case of extreme arching.
The contactor is also compact, so it is able to fit into tight mounting spaces; and it is not position sensitive so it can be mounted in any orientation, giving engineers ultimate design-in flexibility. This is of particular benefit for vehicles where internal space is limited or the design/layout is atypical.
The component features large contact gaps, optimised switching dynamics, high performance arc suppression magnets, as well as other measures that help to safely control the switching arc.
Connectors

Electric vehicle connectors connect a vehicle’s various electrical subsystem, they are often placed in parts of the vehicle that are exposed, so need to be sealed against dust and moisture, as well as being heat resistant.
TE’s AMP+ connector range, for example, are completely sealed and able to cope with extreme temperatures: the connectors work at a temperature range of -40 °C to 140 °C, and are all completely dust-proof and water-proof.
The connectors are also able to transfer voltages at particularly high currents. This has been achieved by increasing the distances between conductive materials.
With very high voltages being conducted, the connectors need to be safe to handle – this is fundamental to the function of an EV connector. The TE high voltage connector range offers voltage levels of up to 850V while being finger actuated and touch-safe, and requiring no external tool to unmate.
As voltages increase, year on year, connectors such as these will become the focus for designers and engineers alike, enabling them to push the limits of what specialist EVs are able to achieve.
Relays
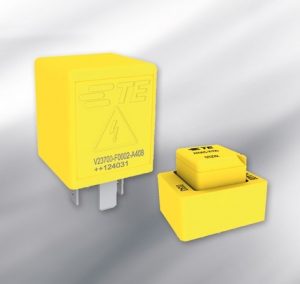
Relays support the connection and disconnection of the traction battery in switching assemblies for hybrid and battery electric vehicles. In high voltage machines, relays need to reliably disconnect the precharge circuit and traction battery, even under fault conditions.
A Mini K HV is a good example of a pre-charge relay designed specifically to meet high voltage requirements; it has two arc extinguishing magnets for improved safety and is suitable for voltage levels up to 450VDC, with precharge currents and limiting break currents up to 20 Amps.
What’s more, is that this relay is a small package and PCB mount, so is ideal for use in hybrid and electric vehicles where weight reduction and space utilisation is crucial.
Manual Service Disconnects
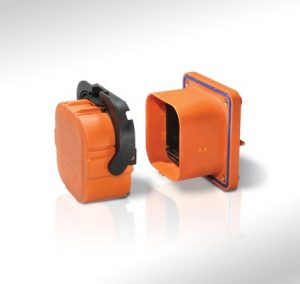
Disconnects are a vital component for any high voltage design. They protect service technicians, emergency response teams and engineers when working on vehicles with extreme voltages.
TEs AMP+ Manual Service Disconnect Plug is made to be suitable for high voltage machines. The solution makes it easy for users to disconnect the internal high voltage battery as well as protect the batteries high voltage cabling from short circuit. It offers a voltage rating of up to 450V with a fuse switch, and up to 1000V with an integrated shunt switch.
This particular disconnect operates at temperatures of -40 to 85 degrees. This is crucial as battery cells generate high temperatures, and even prone to fires and explosions; the higher the volts, the more crucial it is that disconnects are fully operational at high temperatures.
Terminals
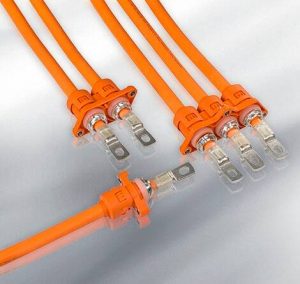
The terminal is a connection point which conducts from the vehicle’s power source, and provides a connection to external circuits. In a specialist EV, the terminal might be responsible for connecting battery cells to onboard electrical devices.
It is important to choose the right terminal type, so that the component can safely act as a conductor for a high voltage power source. This means the terminal needs to be high voltage ready: enter the AMP+ terminal series, which have a rated voltage of up to 800VDC.
While voltage ratings are important, it is also crucial that terminals perform well in harsh conditions. As we move towards a higher voltage future, specialist EVs are becoming more and more ubiquitous – which means they will be used in more testing environments.
High voltage terminals, like those in the AMP+ series, are therefore made with a robust housing design and feature a screwed aggregate connection which achieves a high level of vibrational performance; making them perfect for any high voltage specialist EV design.
Best-in-class
Getting your component selection right, is crucial. State-of-the-art electrical components, built specifically for a specialist market, help ensure best-in-class performance without sacrificing safety or durability. These innovative parts not only ensure your vehicles are designed for the voltage levels of today, but are able to handle the higher voltages of tomorrow.
Are you starting a high voltage electric vehicle project? Do you want to find out more about how electric vehicle components are able to deal with higher voltages? At Dalroad, we stock a range of components which are made specifically for this purpose. To ensure you choose the correct components, that are not only fit for purpose, but durable enough to perform even in the harshest conditions – get in touch with one of our experts at Dalroad here.