Connectors have so far proven critical components in the race towards automotive electrification. They play a fundamental role in the move from fossil fuel to electricity by allowing electric power to flow safely and reliably through the multitude of systems within an EV or hybrid-electric HEV, whilst offering the ease of maintenance required for specialist vehicles. Beyond this, their versatility opens up a host of future applications, from advanced sensors and cameras towards autonomous driving systems. Read on for an overview of how innovations in EV connectors are looking to enable an electric future for specialist vehicles.
Increasing miniaturisation
Miniaturisation has, and always will be, a primary concern for the automotive industry. Increasingly stringent regulations, like the EU’s CO2 emission targets for heavy vehicles, are necessitating a new process of vehicle design; vehicles require optimal space use and component selection.
Fortunately, increasingly innovative connectors are allowing engineers to optimise space use, whilst reducing weight – all resulting in greater efficiency and fewer emissions. TE Connectivity’s (TE’s) 0.50 Series Connectors demonstrate how miniaturised connectors support developments in other car components. By experimenting with tin-based connectors, TE were able to reduce the previous 0.64 Series Connectors size by 70% and weight by 50% without compromising on reliability or performance. This meant that even in high density systems where space was at a premium, complex electric parts involving fuel injection, navigation, power management and more could be connected into ‘blackbox’ networks: smarter functioning without excess weight, all through miniaturised connectors.
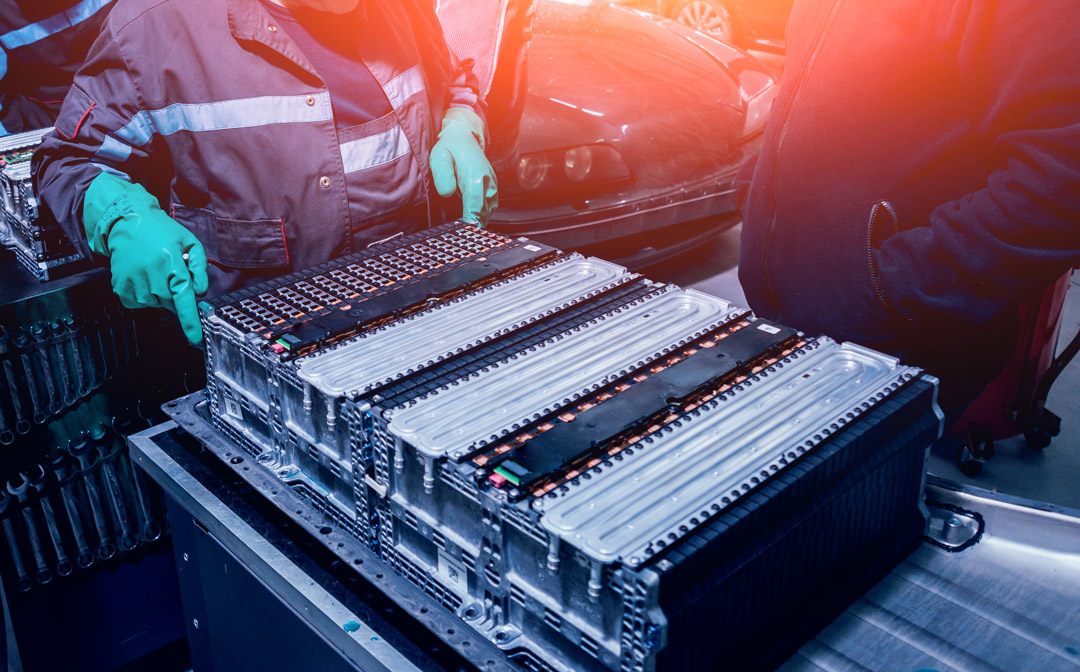
Lightweighting
Linked to miniaturisation is lightweighting: finding innovative ways to make parts lighter, thus reducing the mass of a vehicle, without compromising performance. In specialist vehicles, lightweighting components poses a particular challenge: components are exposed to extreme temperatures and vibrations, but must remain resilient.
For EV connectors, a range of techniques have been used to ensure automobile grade resilience at increasing light weights: introducing smaller wire cross sections within connectors, modified thermoplastic materials and new forms of tab contact have already been used to lower weight without compromising on robustness.
Power optimisation
Making sure that components are making the most of the power available to them is a major concern for the future of EVs and hybrids. In particular, working to ensure that the charge connection is as efficient as possible will receive a lot of attention in the coming years. With current technology, EVs make use of about 80% of the electricity applied to them at the source (compared to around 50% for petrol engines). Work to close that gap will come about from ensuring the sealing performance and resilience of the charge connection over time, as well as the efficiency of the connections within the EV.
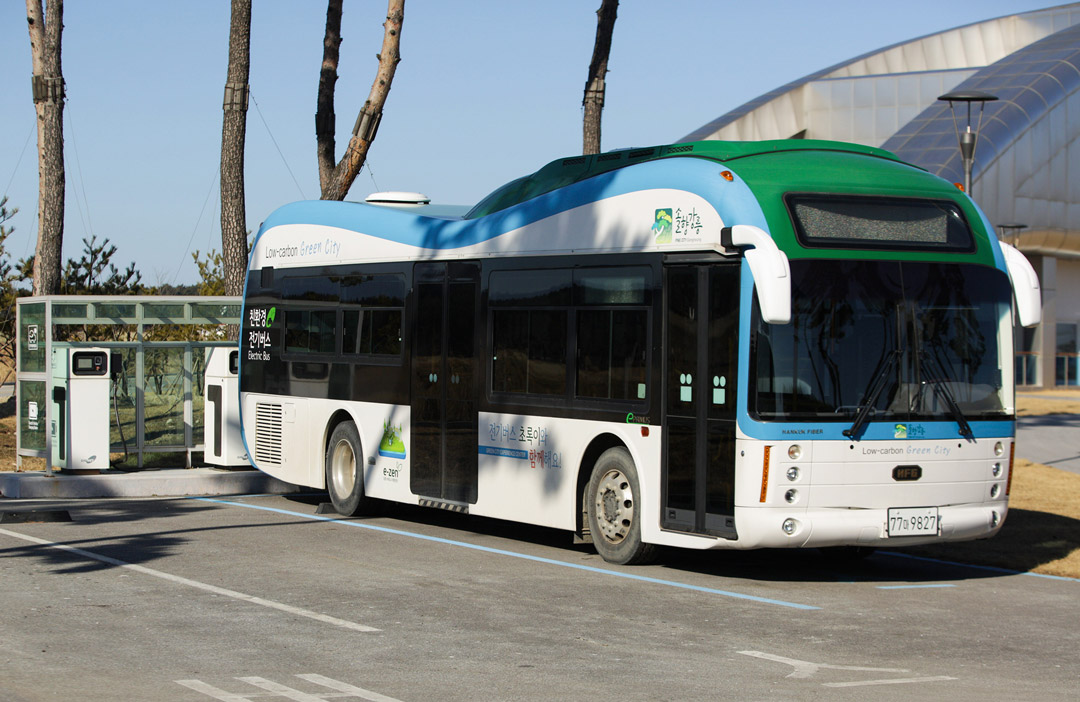
SMART connectors
Electric connectors are capable of much more than allowing power to flow through the various systems of an EV. They can also enable data and radio signals to be transferred across various smaller-scale systems of closed loops comprised by any of the vehicle’s components. Tyre pressure could be altered according to sensors on the chassis, brakes and accelerators to ensure maximum efficiency.
In a fully electric vehicle incorporating sensors into these loops could produce further automation. For example, GPS sensors and accelerators could communicate with each other to prepare for blockages in traffic, or chassis sensors identify rain and trigger the vehicle’s windscreen wipers. Incorporating connected sensors within existing specialist EV connectors could accelerate the movement towards the internet of vehicles for enhanced traffic and fleet management.
This has potential applications even outside EVs: an electric network of sensors across a truck could guide engine operation by measuring pressure, level, temperature, urea quality, and humidity to minimise emissions and ensure maximum efficiency.
Autonomous driving systems
Automotive industry commentators are captivated by the thought that one day, we’ll get into a vehicle without a steering wheel, and perhaps tell a voice-activated driver where we want to go. While this sort of technology is in its infancy, there are innovative solutions that allow us to alleviate some of the bugbears of everyday driving.
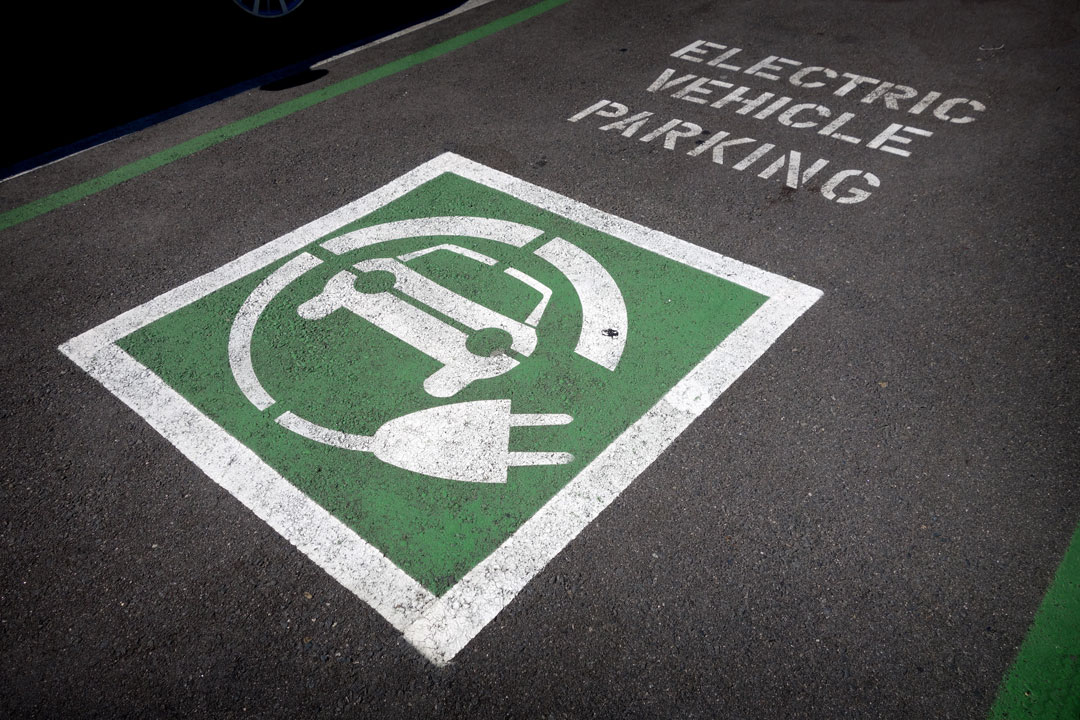
Intelligent connectors are already allowing for mass data transfer (gigabits of data) throughout vehicular systems, delivering valuable insights to fleet managers, drivers, nearby vehicles, insurers and even city planners. Data helps make vehicles safer, greener and more connected.
Even before fully autonomous driving (level four or level five), connectors can ensure an image-feed from a camera on the rear of a vehicle is displayed on a monitor by the driver, with useful information from other sensors around the vehicle (such as distance and acceleration) readily displayed. Having the right connectors in place is the key to ensuring such new technologies can be relied upon.
Connecting with the future
The sheer range of EV connectors available today welcome all sorts of potential applications, allowing for optimised performance, deeper insight into a vehicle’s operation, and new ways for a vehicle’s components to interact with each other. EV connectors establish networks that allow your vehicles to start embracing the efficiency of electricity.