Few things in the world of electrical assembly seem more straightforward than crimping wires to terminals. Insert or place a stripped wire into the short metal barrel (open or closed) and tightly compress to form a homogeneous bond. Needing no solder, heat or flux, the simplicity and speed of the process is why, after more than 70 years, the solderless terminal continues to be one of the most popular and cost-effective connection systems available. However, there’s more complexity to the solderless terminal than meets the eye and the failure of an undetected bad crimp can seriously undermine the integrity of the whole product. An improper crimp can overheat, affect electrical connection, increase scrap, lead to product reworking, and possibly even lead to catastrophic failure. With the high-voltage cable assemblies used in electric and hybrid vehicle systems, achieving a good crimp is a serious issue and industry leading manufacturer TE Connectivity’s authorised distributor in the UK, Dalroad, is keen to spread the word.
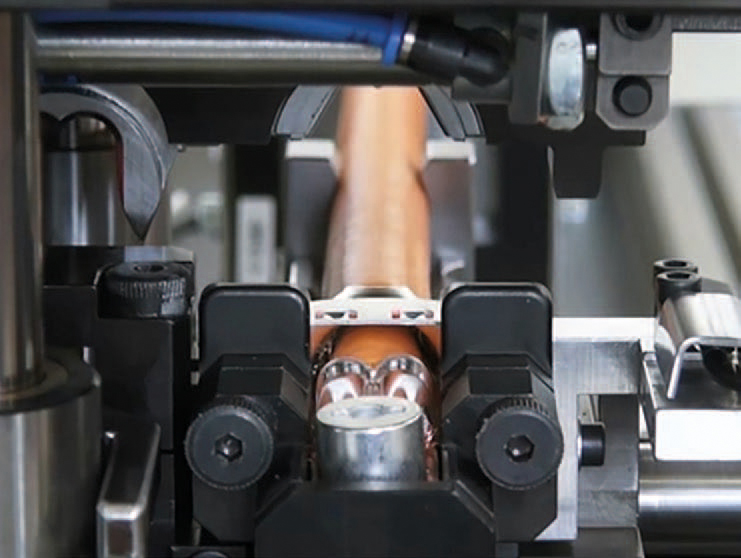
A common misconception is that any tool can be used to crimp a terminal. On the contrary, crimping solderless terminals is a carefully
engineered solution. Tool and terminal are designed to act in tandem, creating crimps that optimize electrical and mechanical performance. Too loose a crimp will result in poor mechanical performance and electrical conductivity. Too tight a crimp may improve electrical performance up to a point, but can damage the terminal body or wire strands, reducing tensile strength and/or vibration resistance. Any of these issues can cause the product to malfunction or fail, resulting in lost production time, damage, repairs, and potential injury and/or litigation.
To consistently achieve quality terminations, TE Connectivity advocates a step-by-step, systematic approach – which covers quality training, wire, terminal, tooling, documentation and inspection – and cautions that failure to address any one of these issues can, and often will, undermine the effectiveness of a crimp. HV assemblies must consist of the correct cable, stripped and matched with the correct HV terminals and connectors which have the features needed to take the system to production. Critical to the crimping process, the tooling must be designed specifically to accept the precise terminal and wire combination. Documentation specifying the measurements and parameters must be carefully observed and followed by close inspection of the finished crimp.
This advice is underpinned by industry safety and certification agencies such as UL and CSA which, as part of the process of certification, conduct tests on solderless terminals for crimp height (a non-destructive method of checking the quality of a good crimp), vibration tests, thermal testing, tensile strength, dielectric strength, and voltage drop in controlled laboratory conditions, according to manufacturers’ instructions. Often misinterpreted, approval depends on the product being used in accordance with the certification criteria, which in the case of solderless terminals, involves crimping using only the specified tool. For instance, a UL-certified crimp requires a UL-certified terminal and the associated UL-certified tool.
Available from Dalroad, TE Connectivity’s ever-expanding portfolio of high-voltage products designed specifically for hybrid and electric vehicles includes five classes of wire – from 2.5mm2 to 120mm2 (20-400A) – and terminals and connectors. Stripping and crimping tools range from handheld for smaller wire cross sections and low production runs, handheld pneumatic for mid-range wire cross-sections, and hydraulic presses for forming larger products. In the UK, TE holds quality training courses on all aspects of crimping solderless terminals, either at its base in Swindon, Wiltshire, or at customer premises at sites across the country.
Read our crimping terminal article in the January issue of the Electric and Hybrid Vehicle Technology International Magazine.